- Tesla's batteries focus on high-energy density and performance, while BYD's prioritize volume efficiency and cost-effectiveness.
- BYD's design allows for better thermal management. Both batteries lack silicon in their anodes and use laser welding for electrode connections. Despite differences, they share similar passive component fractions.
- These insights provide a benchmark for future EV battery design and optimization.
Two main manufacturers dominate the EV (electric vehicle) market: Tesla, which is most popular in Europe and North America, and BYD, which leads the Chinese EV market. However, both manufacturers have released limited data about their batteries, so the mechanical structure and characteristics of these battery cells have remained mysterious.
To compare the batteries used by each manufacturer and better understand how EV batteries function overall, a team of researchers took one of each apart.
The results, published on March 6 in the journal Cell Reports Physical Science, show that Tesla’s batteries prioritize high-energy density and performance, whereas BYD’s batteries prioritize volume efficiency and lower-cost materials. Overall, the study revealed that BYD’s battery is more efficient because it allows easier thermal management.
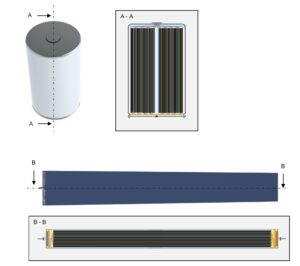
Graphic rendition of the 4680 Tesla Cell (silver cell in the picture) and BYD Blade Cell (blue cell in the picture), including cross sections of both cells. (Jonas Gorsch)
“There is very limited in-depth data and analysis available on state-of-the-art batteries for automotive applications,” said Jonas Gorsch, a researcher at Production Engineering of E-Mobility Components at RWTH Aachen University in Germany and lead author of the study.
To address this, the researchers looked under the hood of Tesla’s battery—the Tesla 4680 cell—and BYD’s battery—the BYD Blade cell—and focused on the specific design and performance features of each. They assessed the mechanical designs and dimensions of the cells, the exact material compositions of their electrodes, and the cells’ electrical and thermal performances. They also deduced the processes used to assemble the cells and the costs of the materials used to make them.
“We were surprised to find no silicon content in the anodes of either cell, especially in Tesla’s cell, as silicon is widely regarded in research as a key material for increasing energy density,” said Gorsch.
The team found that the two types of batteries had significant differences in the speed at which a battery charges (or discharges) relative to its maximum capacity.
The researchers also discovered that the BYD Blade employs a different method of keeping the electrode sheets in place—by using an electrode stack featuring a novel processing step to laminate the edges of the separator that sits between the anode and the cathode. The Tesla battery also uses a novel binder—a substance that holds together the active materials in the electrodes—in comparison to those used by most manufacturers in the industry.
The batteries also showed unexpected similarities: both use an unusual way of connecting their thin electrode foils: with laser welding instead of ultrasonic welding, used by many others in the industry. Also, although the BYD cell is much larger than the Tesla cell, the fraction of passive cell components—such as current collectors, housing, and busbars—is similar.
The results of this study illuminate how Tesla’s battery—the Tesla 4680 cell—and BYD’s battery—the BYD Blade cell—achieve two “highly innovative” but “fundamentally different” design approaches, says Gorsch. Further studies are needed to determine the impact of mechanical cell-design choices on electrode performances in EV batteries, as well as the lifespans of the Tesla and BYD cells, he added.
“The findings provide both research and industry with a benchmark for large-format cell designs, serving as a baseline for further cell analysis and optimization,” said Gorsch, adding that the data can help battery-cell developers make informed choices when deciding on format, size, and active materials.
Publication Referenced in the Article:
More information: Jonas Gorsch et al. Contrasting a BYD Blade prismatic cell and Tesla 4680 cylindrical cell with a teardown analysis of design and performance, Cell Reports Physical Science (2025). DOI: 10.1016/j.xcrp.2025.102453.
This article has been adapted from source material published by Provided by Cell Press.
Comments