Colorado — Researchers working at the forefront of an emerging photovoltaic (PV) technology are thinking ahead about how to scale, deploy, and design future solar panels to be easily recyclable.
Solar panels made of perovskites may eventually play an important role amid global decarbonization efforts to reduce greenhouse gas emissions. As the technology emerges from the testing stages, it is a perfect time to think critically about how best to design the solar panels to minimize their impact on the environment decades from now.
“When you have a technology in its very early stages, you have the ability to design it better. It’s a cleaner slate,” said Joey Luther, a senior research fellow at the U.S. Department of Energy’s (DOE’s) National Renewable Energy Laboratory (NREL) and coauthor of the newly published article in the journal Nature Materials. “Pushing perovskite PV toward enhanced sustainability makes more sense at this stage. We’re thinking about how we can make sure we have a sustainable product now rather than dealing with sustainability issues toward the end of its practical life.”
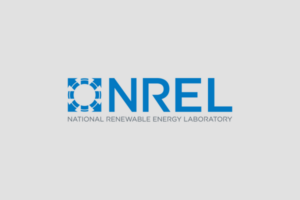
The National Renewable Energy Laboratory (NREL) is transforming energy through research, development, commercialization, and deployment of renewable energy and energy efficiency technologies.
The PV research community, the article noted, is in an influential position to prioritize efforts in remanufacturing, recycling, (aka a “circular economy”) and reliability to make perovskite PV among the most sustainable energy sources on the market.
“Perovskites could unlock the next evolution of high-efficiency PV, and it is our responsibility to assure they are manufactured, used, and recycled sustainably,” said the lead author of the study, Kevin Prince, a former graduate researcher at NREL who is now researching perovskites at Helmholtz Zentrum Berlin in Germany.
Solar panels made from silicon dominate the industry, and while they have enormous environmental and climate benefits, they were not initially designed for “circularity.” The other leading solar technology, cadmium telluride (CdTe), has had an established recycling program from the technology’s inception partly to address the scarcity of telluride. All forms of tech manufacturing come with environmental costs, such as recycling challenges and the use of potentially toxic chemicals. But perovskites are at an inflection point, so the opportunity exists to address those concerns now.
The most efficient circular economy begins at the design stage and considers materials sourcing, strategizes for a long product lifetime, and plans end-of-life management. According to the researchers, the most representative way to assess the environmental impacts of solar panel manufacturing is to look at carbon emissions released during production, embodied energy, sustainable material sourcing, and module circularity.
The journal article identifies critical sustainability concerns for each component of a perovskite solar panel. Lead, for example, could be diluted with other chemically similar metals, such as tin, to lessen the amount of lead in a future panel. However, to date, these substitutions have come at the cost of PV efficiency and durability, requiring much more research before these proposed semiconductors are ready to use in modules. The researchers also suggest that expensive precious metals used in perovskite research cells, including silver and gold, should be replaced with low-cost alternatives, such as aluminum, copper, or nickel, for commercial modules. They also said fluorine-tin oxide would be a more practical material for the cell’s front electrodes rather than the scarcer indium used in indium-tin oxide.
“We want to have the lowest amount of embodied energy in the fabrication,” Luther said. “We want to have the lowest amount of emissions in the fabrication. At this stage, now is the chance to look at those components. I don’t think we have to change anything. It’s more a matter of what decisions should be made, and these arguments should certainly be discussed.”
The authors highlighted different ways to think about the circularity of perovskite panels. Remanufacturing, for example, comes into play when an old module is disassembled with the goal of using certain parts to make a new module. Recycling, meanwhile, calls for the conversion of waste materials into raw materials that can then be refined and reused. One component that requires attention is the specialized glass that provides structural support for perovskite solar modules and offers protection from the elements while remaining very clear to allow in a maximal amount of sunlight. Establishing a recycling pathway for the glass will become more critical as PV deployment grows. Glass manufacturing as it stands today requires raw materials and is an energy-intensive process.
Silvana Ovaitt, a PV researcher and coauthor of the paper, said that as the electricity in the grid itself gets cleaner, the manufacturing of the panels will also be cleaner, further reducing emissions.
“Another concern is the transportation of the final modules and the raw glass because those are the heaviest items,” Ovaitt said. “Local manufacturing will be a great way to reduce those carbon impacts.”
The researchers explain that increasing PV module durability, thereby increasing its useful lifetime, is a more effective approach to reducing the net energy, energy payback, and carbon emissions than designing for circularity alone. Even though a panel can be designed with the end in mind, a longer lifespan means it will not have to be recycled as often.
“Ultimately, we want to make them as durable as possible,” Luther said. “But we also want to consider the aspects of whenever that time does come. We want to be deliberate about how to take them apart and to reuse the critical components.”
The other coauthors, all from NREL, are Heather Mirletz, E. Ashley Gaulding, Lance Wheeler, Ross Kerner, Xiaopeng Zheng, Laura Schelhas, Paul Tracy, Colin Wolden, Joseph Berry, and Teresa Barnes.
The DOE Solar Energy Technologies Office funded the research.
NREL is the DOE’s primary national laboratory for renewable energy and energy efficiency research and development. NREL is operated for DOE by the Alliance for Sustainable Energy LLC.
Comments