- Solar panel efficiencies have been improving, with some panel manufacturers, topping approximately 15-20%.
- Increasing output has one fundamental limitation: mounting. How the panels are mounted is key to extending their life span. Traditional corner mount solutions use the panel frames as an integral part of the support structure.
- Using mounting systems not intended for larger panels can result in degraded system output and a much lower project life span.
Solar panel efficiencies have been slowly improving, topping approximately 15-20% with some panel manufacturers. It would seem as though the most obvious way to increase project power yield and overall system output would be to use higher power panels.
Sounds obvious, right?
You’ve broken the bank and purchased your 600+ watt panels.
Now what?
These new panels are HUGE – in some cases, panels are greater than 2.4m long and 1.3m wide. The frames are also not typically as robust as the older 60-72 cell panels, which solar industry professionals are accustomed to from past projects.
At this point, clients may think they’re cutting down on the panels needed and covering less area to yield more power. It sounds like an optimal situation.
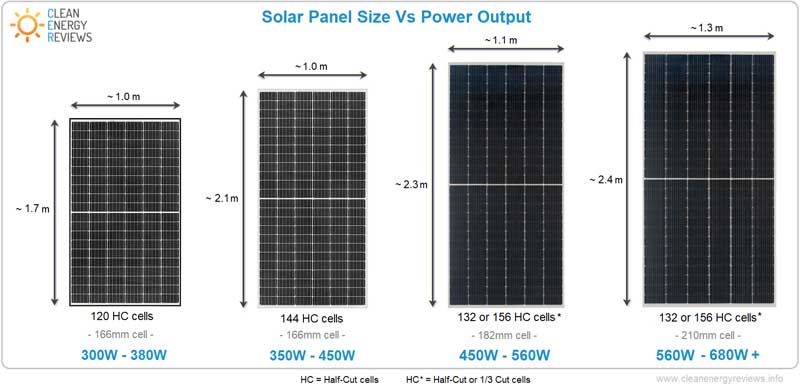
Size Comparison of Module Frames. (Provided by Ed Hutchinson)
So? What’s the catch?
Other than paying more for the panels, it must be made clear that the increase in output has one fundamental limitation: mounting. Clients are left wondering how to ensure the longest possible life span for the key elements of their solar array.
How the panels are mounted is key to extending their life span
Historically, flat-roof racking manufacturers concentrated their efforts on minimizing materials and lowering product costs. From an installation perspective and cost per watt, traditional corner mount solutions (which have been prevalent in the market) made a lot of sense.
As panels continue to grow in size, mounting methods also need to evolve
Traditional corner mount solutions use the panel frames as an integral part of the support structure. As the number of panels has continued to increase, these solutions may provide less than adequate panel support.
Using mounting systems not intended for larger panels can result in micro-fractures, inevitably leading to degraded system output and a much lower project life span.
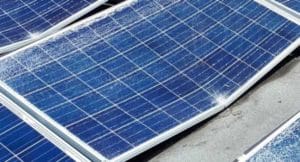
Module Frame Damaged by Snow Accumulation. (Provided by Ed Hutchinson)
These issues are most common in high wind and/or heavy snow load areas. Accumulated snow can cause the panels to crack or sag, and high winds can cause uplift, leading to significant damage over time.
It is always important to check your module manufacturers’ specifications. You will want to verify clamping locations and load tolerances to ensure you don’t void warranty coverage.
How to maximize the life span of modules while minimizing potential issues
Generally, rail-based racking (mounting solutions with full rails supporting the modules) offer the highest level of reliability. These mounting solutions increase the overall rigidity of the module frame, which minimizes the risk of microfractures and offsets the down forces of snow accumulation and wind uplift forces.
Look for mounting hardware vendors that reference Green Zone clamping.
Ensure the module is mounted per the manufacturer’s guidelines. Each manufacturer provides guidelines concerning clamping locations that maximize the integrity of the panel frame.
Long-side clamping, short-side clamping, corner clamping and green-zone rail-based clamping will yield different results.
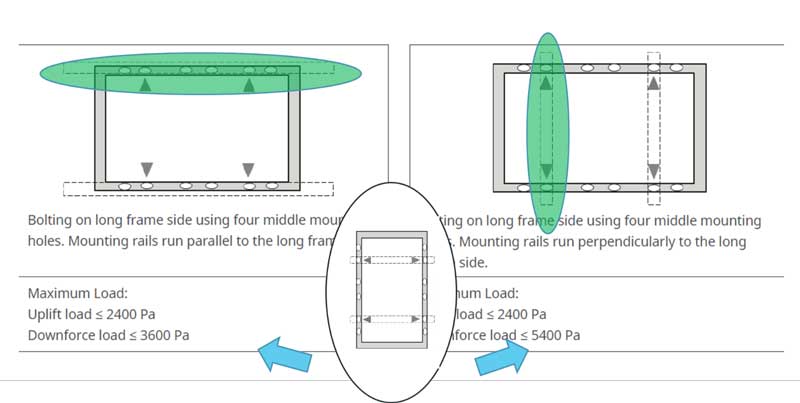
Greenzone Clamping Locations. (Provided by Ed Hutchinson)
Remember that even if your modules are covered under the manufacturer’s warranty, inadequate support may lead to lower system performance, system downtime, and potential module replacements.
Quality mounting products often cost more upfront but will protect your panel investment for much longer.
As the late Ron Popeil once said, you want to “set it and forget it” – build it, do annual maintenance, and enjoy the sunshine.
However, as with most long-term assets, an ounce of prevention is worth a pound of cure.
Comments