Silicon represents 27.7% of the earth’s crust, making it the second most abundant substance after oxygen. This plentiful material is a hard metalloid, and in crystalline form, is characterized by a metallic lustre.
Silicon metal‘s stable tetrahedral configuration makes it incredibly useful in a wide range of industries, such as aluminum, where it’s used to strengthen alloys, personal electronics, where it’s used as a semiconductor, and cosmetics, where it’s used in hair conditioners and face washes, among other things.
In the past few years, electric automakers have pivoted towards silicon, a growing trend that sends the message that the transportation market is quickly favouring electrification. Li-ion batteries that are poised to power this market are also rising sharply in demand.
The global EV battery market is expected to hit 1 trillion dollars in market value by 2030. With so much at stake, a technological race has sparked between battery manufacturers. The race involves developing pathways to find efficiencies, cut costs, and boost EV battery performance, and silicon well positioned to become the key material needed to achieve the high performance required from next-generation Li-ion batteries.
The metalloid is far more energy-dense than graphite (9-10x to be exact!), meaning it holds more Lithium ions and is, therefore, more efficient as an energy storage material. Far less silicon is needed, relative to graphite, to achieve the same storage capacity. This reduces the overall cost of the battery supply chain in addition to negative environmental externalities, as fewer minerals are needed to supply the battery demand.
The abundance of silicon makes it a highly economical choice for battery manufacturers looking for the next breakthrough, and several companies have already begun to compete for just that.
General Motors (GM)
GM, for example, has begun experimenting with a variety of battery chemistries and manufacturing processes to slash production costs. One of these experiments has been with silicon-rich lithium metal for their next-generation of Ultium batteries, which are projected to be finished in 2025.
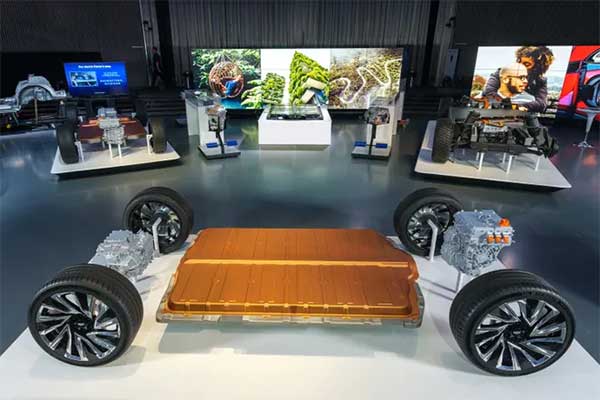
General Motors reveals its Ultium at the Design Dome on the GM Tech Center campus in Warren. General Motors’ Ultium battery technology roadmap includes silicon anodes and lithium metal anodes, which will improve vehicle range, affordability and reduced dependence on rare and costly metals. It is already demonstrating automotive-grade durability and significantly higher energy density. (The Detroit News)
The company has repeatedly made it clear that they feel as though EV battery cost has replaced horsepower as the vital issue that will determine the winners and losers in the EV market.
The company aims to reduce the manufacturing cost of their Li-ion batteries to “well under $100/kWh by 2025,” a dramatic drop from the current price of $150/kWh. GM estimates that these battery improvements will provide their vehicles with a range of between 805-965 kilometres on a single charge, drastically more than EVs on the market today.
Part of GM’s commitment to silicon is borne out of the company’s desire to reduce dependence on precious metals, such as nickel and cobalt. Whereas silicon reserves are plentiful, many of the world’s accessible mineral deposits have already been depleted to some extent, translating into higher procurement costs.
Porsche
Porsche is another high-profile company that’s committed to using silicon in their future EV batteries, with the Chairman of the Executive Board of Porsche AG, Oliver Blume, saying, “the battery cell is the combustion chamber of tomorrow.” Porsche’s next-generation batteries will initially be limited in production, used only for rare, high-performance vehicles and custom motorsport.
The addition of silicon will enable fast-charging potential that hasn’t yet been seen on the market. Porsche has also committed to ensuring their production chain for high-performance batteries is entirely based in Europe, ensuring a high environmental standard is met.
Though few specifics have been released regarding Porsche’s silicon anode batteries, the company is clearly betting heavily on their success.
Porsche plans to install fast-charging stations equipped with branded lounge spaces and innovative self-service facilities along the busiest motorways in Europe. Each location will feature between six and 12 charging ports with a capacity of 350kW or greater and will join Porsche’s existing European charging network that stands at over 135,000.
Tesla
No conversation about EV battery innovation is complete without the mention of Tesla, and as per usual, the company is well ahead of its competitors when it comes to R&D. Silicon has already been used in Tesla vehicles for a few years.
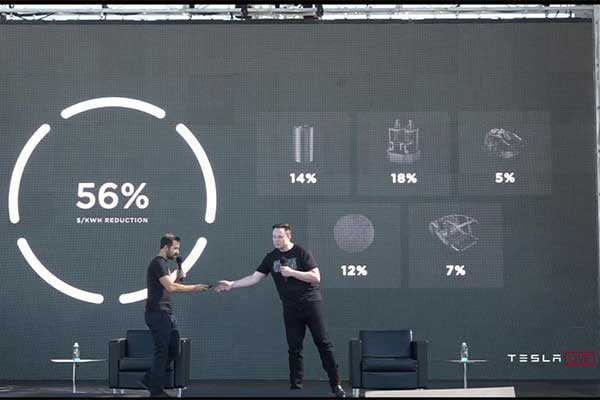
IMAGE: Screen capture from Tesla’s “Battery Day” presentation. The five pillars of Tesla’s strategy to reduce vehicle and battery cost
However, these solutions, such as silicon nanowires, are highly engineered and expensive. As a result, they can’t be scaled. Tesla’s new silicon anode method, dubbed “Tesla Silicon,” costs just $1.20/kWh — roughly 6-10x cheaper than current or other methods used to date. Tesla Silicon begins with raw metallurgical silicon, no engineering required.
The battery is designed to account for the expansion of silicon, rather than constrain it. Tesla describes their silicon as featuring an “elastic binder and electrode design” in addition to an “elastic, ion-conducting, polymer coating.”
These changes alone are projected to increase Tesla’s battery range by 20% and decrease costs by 5% per kWh. One of the most significant benefits of using raw metallurgical silicon is that manufacturing costs can be significantly reduced by forgoing early engineering processes. This also means the solution is easy to scale, as it doesn’t require any high upfront capital expenditures.
As quickly as the vehicle market is moving towards electrification, the EV industry is evolving towards silicon anode batteries. The capacity limitations of graphite make the material ill-suited to underpin a global economic revolution, whereas silicon offers a cheap, abundant, powerful, and environmentally friendly alternative.
Expect to see more automakers join the silicon bandwagon and announce plans for Li-ion battery innovation in the coming months.
Comments