Silicon, also known as silicon metal, is one of today’s strategic materials. It is a chemical element with the symbol Si and atomic number 14. It is a hard, brittle crystalline solid with a blue-grey metallic lustre, and is a tetravalent metalloid and semiconductor.
It is a member of group 14 in the periodic table: carbon is above it; and germanium, tin, and lead are below it.
Silicon-based products comprise a versatile array of applications in the manufacturing industry. Because silicon is easily manipulated and tailored, with high-temperature stability and age resistance, silicon often operates in conjunction with other materials to insulate, purify, soften, adhere, condition, or otherwise protect a product. Silicon-based materials are also used to improve appearance, transfer energy, and aid in reconstruction.
Let’s discuss the different types of silicon states and their applications in industry.
Metallurgical Grade Silicon
For silicon to be considered metallurgical grade, it must exhibit a purity level of at least 98%. Metallurgical grade silicon is the primary raw material used to produce solar grade silicon and is a crucial stepping stone in the refining process of silicon metal.
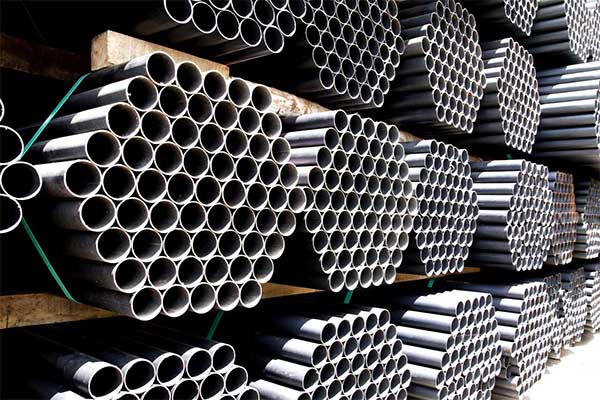
The steel and aluminum industries are good examples of the metallurgical industry.
Producing metallurgical grade silicon is achieved by reacting highly pure silicon with wood or charcoal in an electric arc furnace. It is used extensively in metallurgical industries, which work with metallic alloys. The steel and aluminum industries are good examples of the metallurgical industry.
Predominantly, metallurgical grade silicon is used for aluminum casting to develop aluminum alloy products.
The single most abundant use of metallurgical grade silicon is for the automobile industry, which represents a slight majority, or 55% of all metallurgical silicon used industrially. Aluminum is a choice metal as it’s durable, reliable, and lightweight. When combined with metallurgical grade silicon, the positive properties of aluminum are further enhanced, producing a highly efficient alloy.
Electric vehicles are positioned to take advantage of these highly efficient aluminum alloys, as their body, engines, wheels, and screws are all able to be produced using such materials.
The rapidly rising demand for electric vehicles has positively impacted the market strength of related industries, such as aluminum and silicon metal. As economies move further towards global electrification, the demand for such alloys will continue to rise because of their proven consistency and durability.
Chemical Grade Silicon
Chemical grade silicon, when compared to metallurgical grade silicon, represents a step up along the refining process. The purity of chemical grade silicon ranges anywhere from 99-99.99%. The production of chemical grade silicon metal begins with the refining process of silica within quartz rock or sand.
This is followed by a carbothermic reduction of silica that occurs in an arc furnace to produce metallurgical grade silicon. This is then further refined through a hydro-metallurgical process to produce chemical-grade silicon.
The industrial uses of chemical grade silicon are vast. Most of the applications for chemical-grade silicon centers around the production of silicone polymers. These polymers include silicone rubbers, silicon-based oils, and greases, sealants, lubricants, and silicones.
Polymers are macromolecules that are composed of repeating subunits. The repetition of subunits produces significant strength and flexibility within the molecule, meaning polymers have highly adaptable industrial uses. The flexibility of polymers is further enhanced because they can exist in both natural and synthetic forms.
Silicones are an example of a synthetic polymer made up of siloxane, which is a chemical compound derived from silicon. They are frequently used in construction, namely for sealants, adhesives, and lubricants. The healthcare, cosmetic, electronics, packaging, and photovoltaic industries also utilize silicone products for various purposes. Silicones are non-reactive with most chemicals, allowing them to be used internally and externally within the field of medicine.
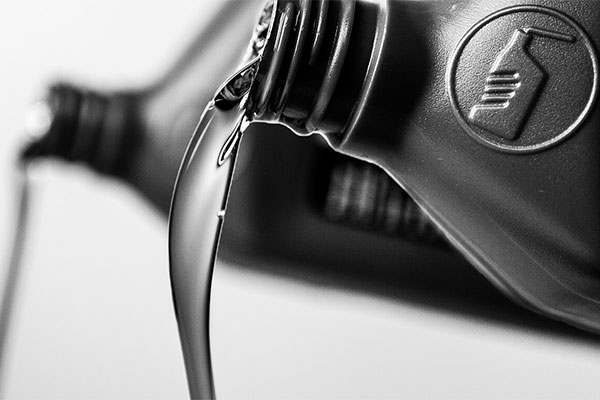
Silicones are an example of a synthetic polymer made up of siloxane, which is a chemical compound derived from silicon.
Silicone is used in long term implantations, as well as to assist medical device technologies. Prosthetic limbs, artificial joints, medical adhesives, molds, and tubing also represent prominent medicinal uses for silicone products.
The non-reactive nature of silicones enables cosmetic products to take advantage of the material. Silicones are often used in leave-on skincare products and all manner of hair products. Scar-healing and soothing agents also feature silicone, as the material is non-irritating and widely applicable for the vast majority of the population.
Silicones are also prevalent within the packaging industry, namely food packaging, and processing. They are safe in food applications, as silicones don’t modify food properties and can be produced to be odorless.
The photovoltaic industry is another primary user of silicon and silicones. Photovoltaic technology refers to equipment that is capable of converting light into electricity using semi-conductive materials. Solar panels represent the most obvious example of this technology and are most frequently produced using silicon solar cells.
Silicon-based solar panels represent roughly 90% of solar modules on the market. The solar and wind industries rely heavily upon silicon as a raw material. Not only do solar panels utilize silicon within their design, but silicone sealants and adhesives are also used to put solar modules together. Wind turbines also frequently use these industrial adhesives and sealants during construction.
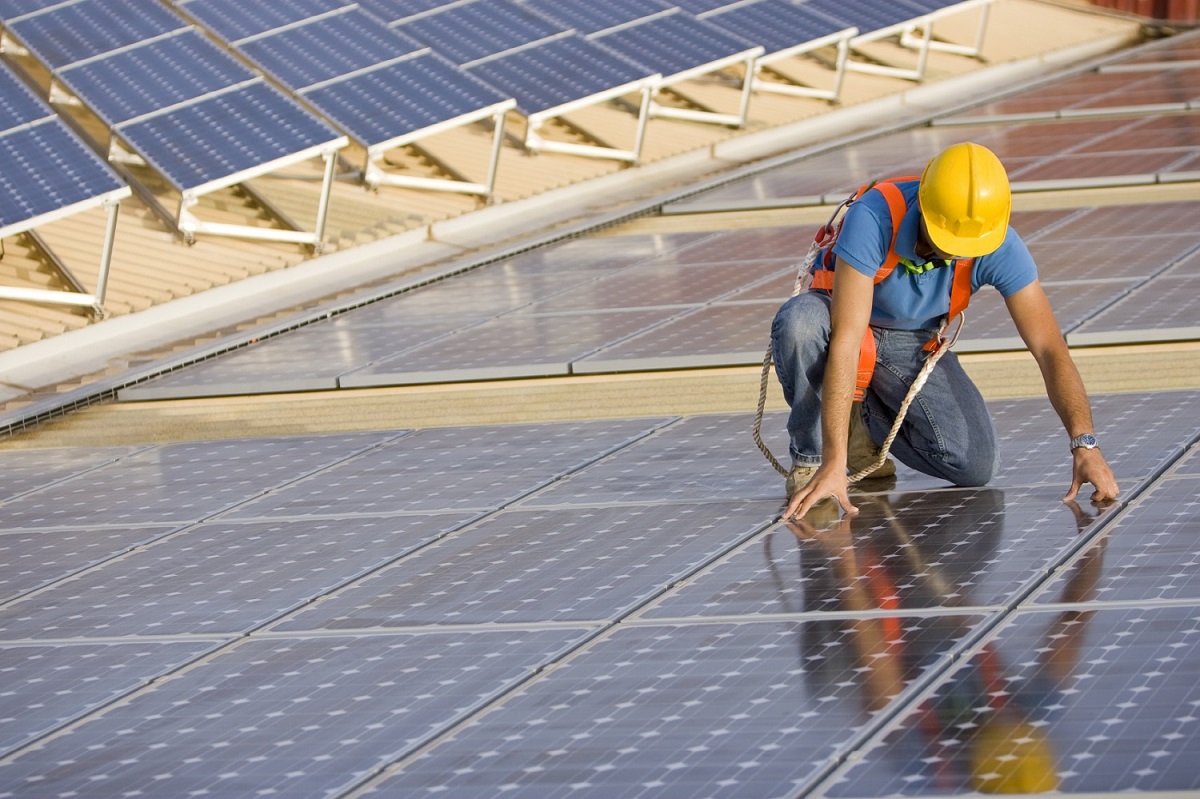
A PV module is an assembly of photovoltaic cells mounted in a framework for installation. Photo-voltaic cells use sunlight as a source of energy and generate direct current electricity. A collection of PV modules is called a PV Panel, and a system of Panels is an Array. Arrays of a photovoltaic system supply solar electricity to electrical equipment.
The amount of electricity produced by a solar installation depends on a combination of the quality of light (intensity & wavelengths) as well as multiple performance indicators of the panel’s solar cells. The greater the purity of silicon used in solar cells, the more efficient they are in converting sunlight into electricity. This, in turn, creates more efficient and cost-effective solar modules.
Silicon for Batteries
Silicon metal has massive potential for improving standard lithium-ion (li-ion) battery performance. Incorporating silicon, rather than graphite into the battery anode, can massively enhance battery efficiency. Innovation surrounding silicon anode technology is promising.
Silicon exhibits a far greater energy density than graphite, which enables a higher concentration of energy to be stored on the same sized (or smaller sized) battery part. This is critical to the energy storage industry, as battery efficiency is key to the cost-effectiveness and market strength of such an industry.
The implications for using silicon in batteries are expansive, with faster charge times (up to 10x the current speed), charges which deplete slower, and more substantial overall charges providing ample opportunity for growth in energy storage and related industries.
Clean energy would be the most notable industry boosted by such a dramatic development in battery technology.
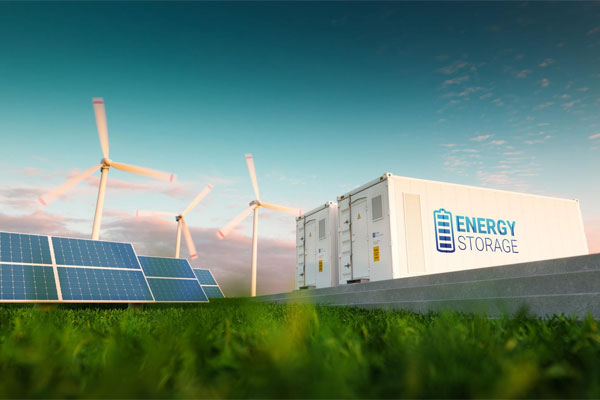
Grid energy storage (large-scale energy storage) is a collection of methods used to store electrical energy on a large scale within an electrical power grid. Electrical energy is stored during times when production (especially from intermittent power plants such as renewable electricity sources such as wind power, tidal power, solar power) exceeds consumption, and returned to the grid when production falls below consumption.
Wind and solar power are considered intermittent energy sources — meaning they produce electricity less reliably than traditional fossil fuels. There is no solar energy production during the night time, much like there is no wind energy produced when there is no wind. These energy sources rely on the ability to store collected energy, meaning until energy storage applications are improved upon, battery restrictions will continue to represent a salient barrier for green energy.
Regardless, it’s becoming clear that the energy storage capabilities of silicon metal have the potential to revolutionize the global energy economy.
But for Silicon to fulfill the Renewable Energy Revolution (“RER”) presently underway, high purity silicon is needed, as silicon does not exist in its pure state; it must be extracted from quartz (SiO2), in what has historically been a capital and energy-intensive process.
Here is where HPQ Silicon comes in.
Since 2015, HPQ Silicon has been developing the PUREVAP™ Quartz Reduction Reactor (QRR) Project. The project is an innovative process (patent pending), which will permit the one-step transformation of quartz (SiO2) into high purity silicon (Si) at reduced costs, energy input, and carbon footprint.
Comments