As NASA’s Parker Solar Probe spacecraft begins its first historic encounter with the sun’s corona in late 2018 — flying closer to our star than any other mission in history — a revolutionary cooling system will keep its solar arrays at peak performance, even in extremely hostile conditions.
Every instrument and system on board Parker Solar Probe (with the exception of four antennas and a special particle detector) will be hidden from the sun behind a breakthrough thermal protection system (TPS) — an eight-foot-diameter shield that the spacecraft uses to defend itself against the intense heat and energy of our star.
Every system will be protected, that is, except for the two solar arrays that power the spacecraft. When the spacecraft is closest to the sun, the solar arrays will be receiving 25 times the solar energy they would while orbiting Earth, and the temperature on the TPS will reach more than 2,500°F (1,370°C). The cooling system will keep the arrays at a nominal temperature of 320°F (160°C) or below.
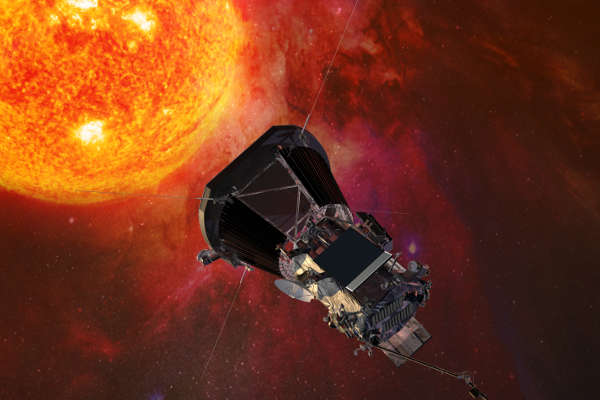
The solar panels are shown here on this artist rendering of Parker Solar Probe; they are the black squares with gray rectangles on the center of the spacecraft.
Credit: NASA/JHUAPL
“Our solar arrays are going to operate in an extreme environment that other missions have never operated in before,” said the Johns Hopkins Applied Physics Lab’s Mary Kae Lockwood, spacecraft system engineer for Parker Solar Probe.
New Innovations to Survive the Inferno
The very outermost edges of the solar arrays are bent upward, and when the spacecraft is closest to the sun, these small slivers of array will be extended beyond the protection of the TPS in order to produce enough power for the spacecraft’s systems.
The incredible heat of our star would damage conventional spacecraft arrays. So, like many other technological advances created especially for this mission, a first-of-its-kind actively cooled solar array system was developed by APL, in partnership with United Technologies Aerospace Systems (UTAS) in Windsor Locks, Connecticut (which manufactured the cooling system), and SolAero Technologies of Albuquerque, New Mexico (which produces the solar arrays).
“This is all new,” Lockwood said of the innovations related to the actively cooled solar array system. “NASA funded a program for Parker Solar Probe that included technology development of the solar arrays and their cooling system. We worked closely with our partners at UTAS and SolAero to develop these new capabilities, and we came up with a very effective system.”
The Parker Solar Probe cooling system has several components: a heated accumulator tank that will hold the water during launch (“If water was in the system, it would freeze,” Lockwood said); two-speed pumps; and four radiators made of titanium tubes (which won’t corrode) and sporting aluminum fins just two hundredths of an inch thick. As with all power on the spacecraft, the cooling system is powered by the solar arrays — the very arrays it needs to keep cool to ensure its operation. At nominal operating capacity, the system provides 6,000 watts of cooling capacity — enough to cool an average-sized living room.
Somewhat surprisingly, the coolant used is nothing more than regular pressurized water — approximately five liters, deionized to remove minerals that could contaminate or harm the system. Analysis showed that, during the mission, the coolant would need to operate between 50°F (10°C) and 257°F (125°C) — and few liquids can handle those ranges like water. “Part of the NASA technology demonstration funding was used by APL and our partners at UTAS to survey a variety of coolants,” said Lockwood. “But for the temperature range we required, and for the mass constraints, water was the solution.” The water will be pressurized, which will raise its boiling point above 257°F.
The solar arrays feature their own technical innovations. “We learned a lot about solar array performance from the [APL-built] MESSENGER spacecraft, which was the first to study Mercury,” said Lockwood. “In particular, we learned how to design a panel that would mitigate degradation from ultraviolet light.”
The cover glass on top of the photovoltaic cells is standard, but the way the heat is transferred from the cells into the substrate of the panel, the platen, is unique. A special ceramic carrier was created and soldered to the bottom of each cell, and then attached to the platen with a specially chosen thermally conductive adhesive to allow the best thermal conduction into the system while providing the needed electrical insulation.
From Ice to Fire: Launch Challenges
While the extraordinary heat of the sun will be the spacecraft’s most intense challenge, the minutes immediately following launch are actually one of the spacecraft’s most critical early performance sequences.
When Parker Solar Probe launches on board a ULA Delta IV Heavy rocket from Cape Canaveral Air Force Station, Florida, in summer 2018, the cooling system will undergo wide temperature swings. “There’s a lot to do to make sure the water doesn’t freeze,” said Lockwood.
First, temperatures of the solar arrays and cooling system radiators will drop from that in the fairing (about 60°F, or 15°C) to temperatures ranging from -85°F to -220°F (-65°C to -140°C) before they can be warmed by the sun. The pre-heated coolant tank will keep the water from freezing; the specially designed radiators — designed to reject heat and intense temperatures at the sun — will also survive this bitter cold, thanks to a new bonding process and design innovations.
Less than 60 minutes later, the spacecraft will separate from the launch vehicle and begin the post-separation sequence. It will rotate itself to point at the sun; the solar arrays will release from their launch locks; the arrays will rotate to point to the sun; a latch valve will open to release the warm water into two of the four radiators and the solar arrays; the pump will turn on; the spacecraft will rotate back to a nominal pointing orientation, warming up the two coldest and unactivated radiators; and power from the cooled solar arrays will begin recharging the battery.
In another first, this complex and critical series of tasks will be completed autonomously by the spacecraft, without any input from mission control.
The water for the two unactivated radiators will remain in the storage tank for the first 40 days of flight; after that, the final two radiators will be activated.
“One of the biggest challenges in testing this is those transitions from very cold to very hot in a short period of time,” Lockwood said. “But those tests, and other tests to show how the system works when under a fully heated TPS, correlated quite well to our models.”
Thanks to testing and modeling, the team studied data and increased the thermal blanketing on the first two radiators to be activated, in order to balance maximizing their capacity at the end of the mission, and further reduce the risk of water freezing early in the mission.
Keeping Cool, Autonomously
When Parker Solar Probe is hurtling past the sun at some 450,000 miles an hour (724,000 KPH), it will be 90 million miles from mission controllers on Earth — too far for the team to “drive” the spacecraft. This means that adjustments to how the spacecraft is protecting itself with the TPS need to be handled by Parker Solar Probe’s onboard guidance and control systems. These systems use new and effective autonomous software to allow the spacecraft to instantly alter its pointing to maximize protection from the sun. This autonomous capability is critical to the operation of the spacecraft’s solar arrays, which must be constantly adjusted for optimal angle as Parker Solar Probe hurdles through the sun’s harsh, superheated corona.
“During solar encounters, very small changes in the wing angle of the solar array can vastly change cooling capacity needed.” Lockwood said that a one degree change in the array angle of one wing would require 35 percent more cooling capacity.
The constant challenge is to make sure the spacecraft and the arrays are staying cool.
“There’s no way to make these adjustments from the ground, which means it has to guide itself,” Lockwood said. “APL developed a variety of systems — including wing angle control, guidance and control, electrical power system, avionics, fault management, autonomy and flight software — that are critical parts working with the solar array cooling system.”
Comments