- The two companies announce the extension of a Development Agreement signed in 2017.
- Main focus on manufacturing and value generation associated with the deployment of Porous Silicon (PSi) in the Lithium-ion batteries market.
- HPQ will have a North American exclusivity over the use of Apollo's patented process to manufacture Porous Silicon.
Montreal, Qc — HPQ Silicon Resources Inc. (“HPQ” – “The Company”) TSX-V: HPQ; FWB: UGE; Other OTC: URAGF; is pleased to announce the extension of the Development Agreement signed in 2017 with Apollon Solar SAS (“Apollon”) from January 1 to June 30, 2020.
The biggest change to this fourth renewal is that the Agreement’s main focus is now on manufacturing and value generation associated with the deployment of Porous Silicon (PSi) in the Lithium-ion batteries market, using Apollon’s patented process to manufacture Porous Silicon Wafers with Silicon Metal (Si) produced by the HPQ PUREVAP™ Quartz Reduction Reactor (“QRR”).
While the agreement is ongoing, HPQ will have a North American exclusivity over the use of Apollo’s patented process to manufacture Porous Silicon. If required, the Parties have already agreed to meet in May 2020 to negotiate an extension.
“HPQ and Apollon are consolidating their collaborations in order to take maximum advantage of our pioneering position in the manufacture of Porous Silicon wafers using PUREVAP™ silicon metal. During 2020, we intend to demonstrate the commercial potential of the technology and Porous material produced” said Bernard Tourillon, President and CEO HPQ Silicon. “Silicon Metal’s potential to meet energy storage demand is undeniable and generating massive investments, as well as, serious industry interest, so our timing could not be better.”
POROUS SILICON – AN ADVANCED MATERIAL WITH CURRENT HIGH-COST CONSTRAINTS
Porous silicon is a Silicon Metal (Si) structure in which Nanopores have been formed by electrochemical etching.
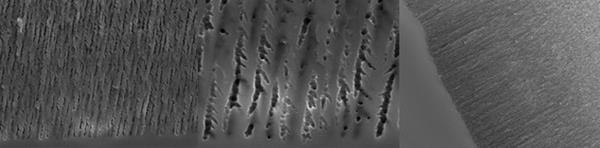
FE-SEM images of Porous Silicon produced by Apollon Solar (HPQ-Silicon Resources Inc.)
Market opportunities for porous silicon are massive, ranging from electronics, batteries, environment, consumer goods, sensors, and medicine, to name just a few. Their high manufacturing cost, since available electrochemical etching processes require electronic-grade silicon (9N to 11N) as raw material, represent a significant barrier to their commercial application.
APOLLON PATENTED LOW-COST PROCESS TO MANUFACTURING POROUS SILICON (PSi) WAFERS
In 2012, Apollon, working in collaboration with France INSA Lyon œœ”) France CNRS (“Centre National de la Recherche Scientifique”), developed and obtained a worldwide patent for a unique low-cost process that uses standard metallurgical Silicon Metal (2N to 4N+ Si) to produce porous Silicon Wafers that can have porous structure sizes of either Microporous (<5nm), Mesoporous (5nm – 50nm) and Macroporous (>50nm) as per end-users requirements.
NDA WITH LITHIUM-ION BATTERY MANUFACTURER LOOKING FOR POROUS SILICON WAFERS
The complement of HPQ and Apollon’s unique capabilities attracted the interest of a next-generation Lithium-ion battery manufacturer looking for a potential supplier of porous silicon wafers. HPQ and partner Apollon, acting as one party, have already signed a non-disclosure agreement (“NDA”) with the battery manufacturer, with discussions and technical information exchanges are now ongoing. The aim of these discussions is to have the technical specifications required in order to provide the battery manufacturer with the Porous Silicon wafers they are looking for as soon as feasible. For competitive reasons, the name of the battery manufacturer will remain confidential for the time being.
GLOBAL ENERGY STORAGE MARKET READY TO EXPLODE
A recent report by Wood Mackenzie Power projects that energy storage deployments are estimated to grow 1,300% from a 12 Gigawatt-hour market in 2018 to a 158 Gigawatt-hour market in 2024. An estimated US$71 billion in investments will be made into storage systems where batteries will make up the lion’s share of capital deployment.
MASSIVE ENERGY STORAGE DEMAND CANNOT BE MET UNLESS SILICON ANODES REPLACE GRAPHITE
The Li-ion battery is the dominant technology in energy storage while graphite, a fairly low energy density material compared to other anode materials, is the dominant anode material in for Li-Ion batteries.
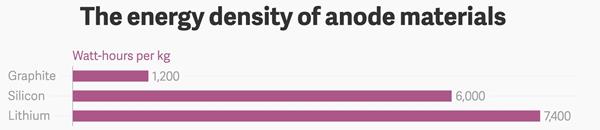
Graph of Energy Density of Anode Materials (HPQ-Silicon Resources Inc.)
Presently, silicon metal powders are blended with graphite to make anodes for Li-ion batteries, resulting in less than 10 wt% Si content in Li-ion batteries. Even with the limited performance improvement achieved to date, demand for Silicon Metal powders is estimated to represent an addressable market of US $ 1B by 20221 expanding at a CAGR of 38.9% between 2019 – 2024.
MANUFACTURING POROUS SILICON POWDERS FOR TRADITIONAL LITHIUM-ION BATTERIES
By crushing porous silicon wafers, it should be possible to make a porous silicon powder that, when combined with graphite, could improve the performance of currently available lithium-ion batteries. Porous silicon wafers (Microporous, Mesoporous, and Macroporous) will be manufactured and crushed into powder. Batteries cycling tests will be carried in order to define and validate the characteristics of the powders produced.
Comments